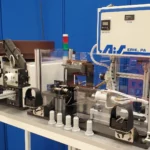
Maximize ROI with AIS’s O-Ring and Seal Installation Machines
February 4, 2025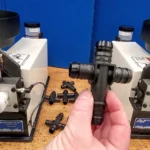
Tailored O-Ring Solutions for Complex Assembly Needs
February 18, 2025The Best Way to Install O-Rings
Why Radial Stretch Matters
In the world of manufacturing and assembly, o-rings may be small, but they play a huge role in preventing leaks, maintaining pressure, and safeguarding overall product quality. However, not all installation methods are created equal. While some organizations rely on outdated techniques or inconsistent tools, at AIS, we champion the radial stretch method. Below, we’ll explore why this method outperforms alternatives, especially finger grippers, and how it delivers greater consistency, durability, and return on investment.
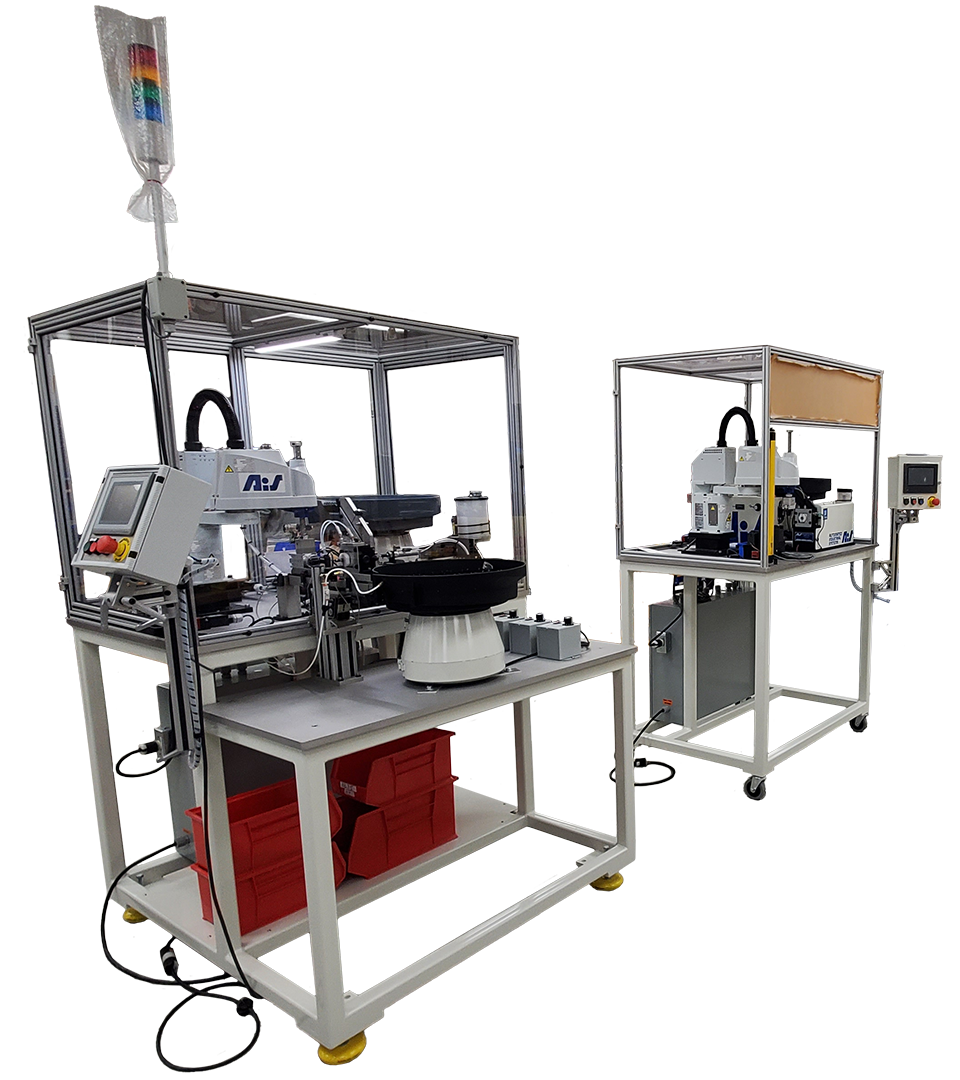
A Brief Overview of Traditional Methods
Manual Slide or Push
Many manufacturers install o-rings by sliding or pushing them into place using hand tools or rudimentary fixtures. This can introduce twisting, pinching, or distortion of the seal. Over time, these small errors can lead to early seal failures.
Cone or Tapered Approach
Some operations use a cone-shaped tool to expand the o-ring, then slide it over a part. While more controlled than manual pushes, it may still result in localized stress if not done carefully. According to o-ring manufacturers, overstretching a seal, even briefly, can create residual stress that shortens its service life.
Finger Grippers
Another approach involves finger grippers, which clamp or pull on the o-ring at limited contact points. This method can create highly uneven stress zones, leading to micro tears or distortions in the material. Any method that overstretches a seal introduces residual stress that degrades its performance. Finger grippers can inadvertently pull the ring beyond its elastic limit in certain areas, making seal failure more likely over time.
Why the Radial Stretch Method Excels
Radial stretch uniformly expands the o-ring from the inside out, maintaining the seal’s cylindrical profile and eliminating localized tension points. By distributing force evenly, you avoid the pitfalls of pinching or distortion that can occur with finger grippers and other methods.
Key Advantages of Radial Stretch
-
Consistent Expansion: Each portion of the o-ring is stretched uniformly, reducing the chance of failure points or micro tears.
-
Less Scrap, Less Rework: Properly installed o-rings lead to fewer defects, saving time and material costs.
-
Longer Service Life: Even distribution of stress extends the seal’s lifespan, reducing maintenance and replacements.
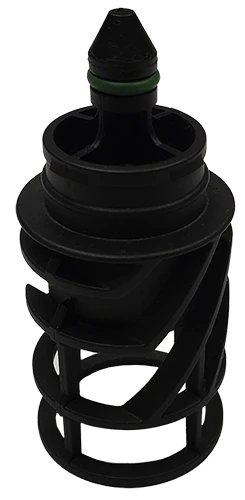
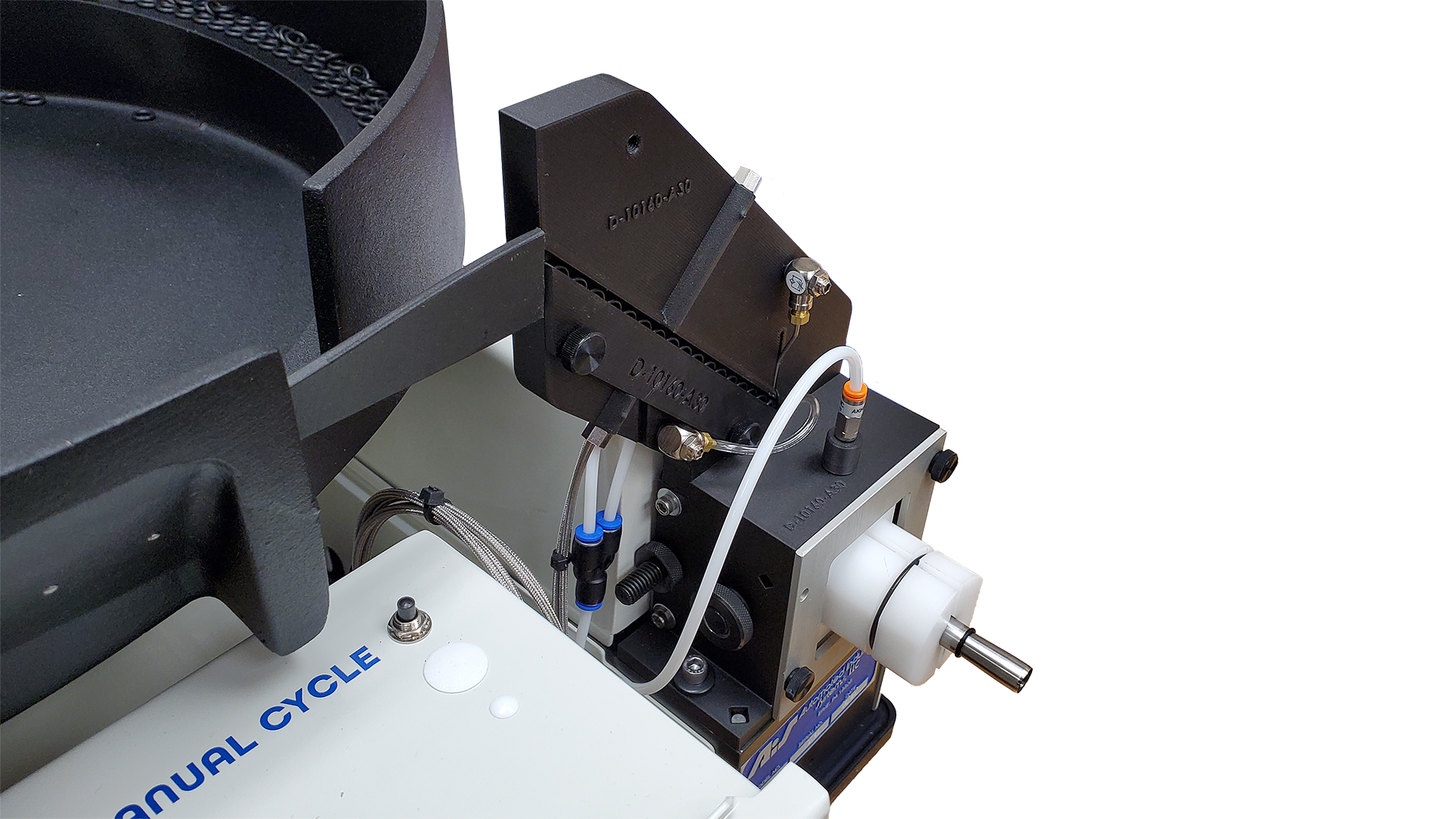
The AIS Difference
At AIS, we leverage the radial stretch method in all of our o-ring and seal installation machines because we know that uniform expansion translates to greater reliability. By combining this method with user-friendly features and robust automation options, our equipment helps manufacturers:
-
Boost Product Quality: Consistently installed o-rings reduce the risk of leaks, preserving your brand’s reputation.
-
Cut Downtime: When seals are installed correctly the first time, you spend less time on troubleshooting and repairs.
-
Adapt Easily: Our machines can handle various materials and o-ring sizes, whether you’re fully automated or using semi-automated processes.
While finger grippers, cones, and manual pushes have their places in certain applications, the radial stretch method stands out as the top choice for manufacturers seeking consistent, long-lasting seals. Backed by industry research and our own extensive experience, AIS continues to refine and perfect this approach—ensuring your operation benefits from optimal seal performance, minimal scrap, and reduced downtime.
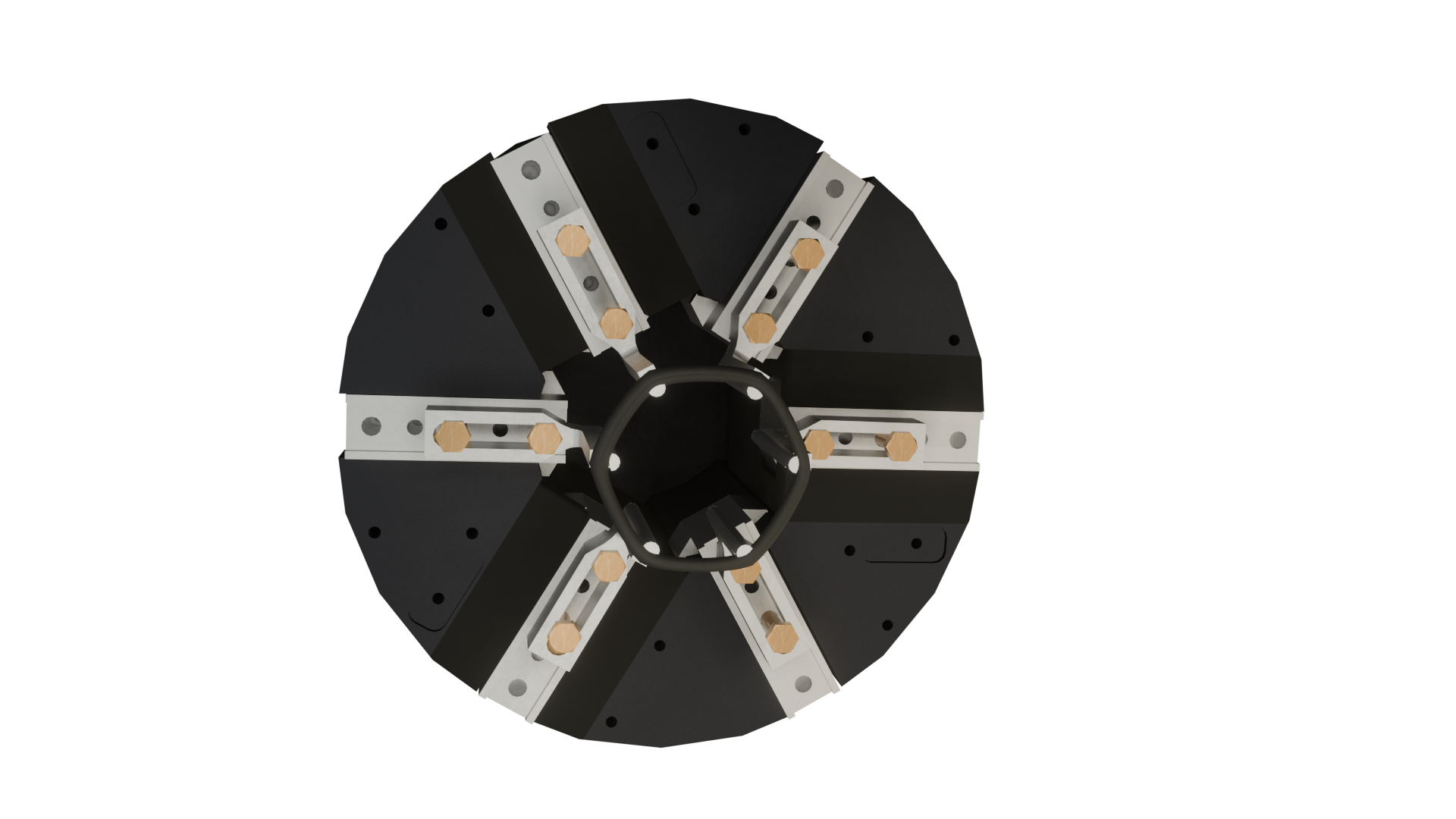