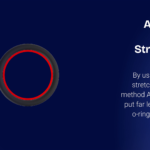
The Best Way to Install O-Rings
February 11, 2025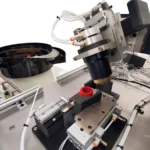
How AIS’s O-Ring Assembly Machines Integrate Seamlessly with Automation
February 25, 2025Tailored O-Ring Solutions
for Complex Assembly Needs
Customer Challenge
Imagine having two similar parts that each require three o-rings, but one also needs a fourth, slightly larger o-ring on one end. For many manufacturers, switching out tools or reconfiguring equipment can bog down production and create a logistical headache. One of our clients faced exactly this dilemma, and they needed a fast, reliable way to handle both parts without frequent downtime.
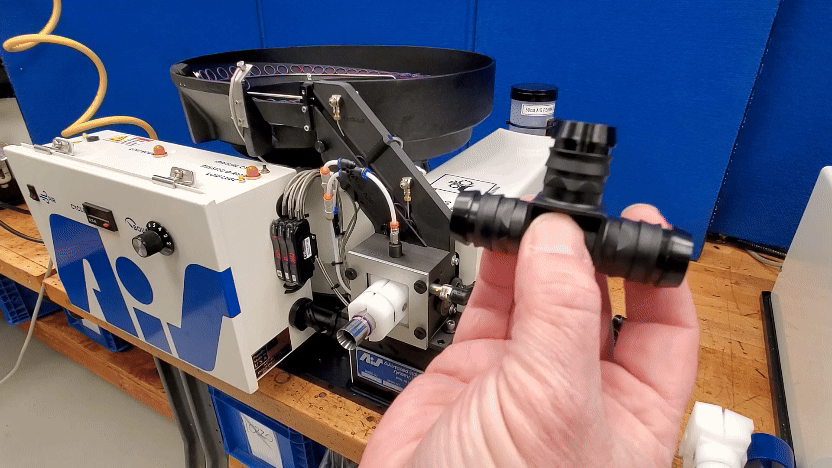
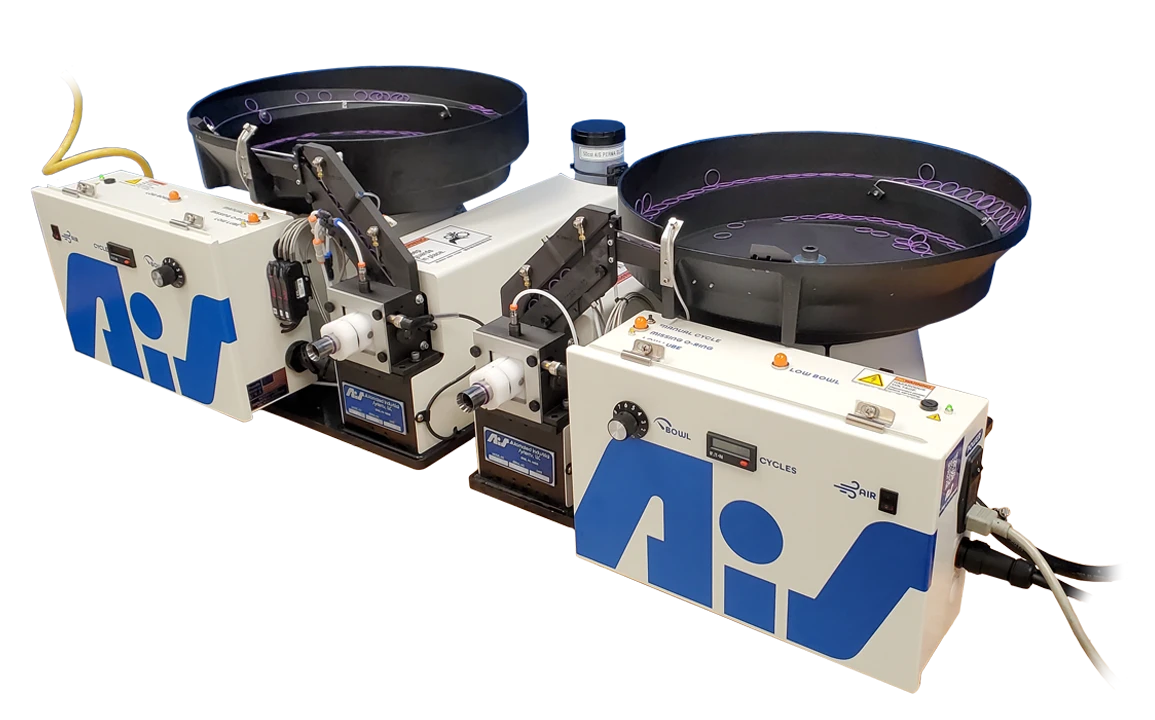
AIS’s Tailored Solution
AIS proposed a two-machine strategy using our ASP-1 o-ring installation machines. The first, a right-handed ASP-1, would install three o-rings on either part. Whenever the part needing the fourth, larger o-ring came through, it would then move to a left-handed ASP-1 for the final seal. Both machines used the same head and mandrel design, which meant the client didn’t need to keep a stash of extra tooling for different dimensions.
Why Two Machines?
-
Maximized Throughput: Rather than stopping production to swap out mandrels and heads, the client could simply route each part to the correct ASP-1.
-
Uninterrupted Workflow: Because the machines sat in the same assembly cell, operators could easily pass one part from the right-handed ASP-1 to the left-handed ASP-1, maintaining a steady output.
-
Quality Assurance: Each ASP-1 was configured for perfect seal placement, reducing human error and preventing leaks or uneven stretches.
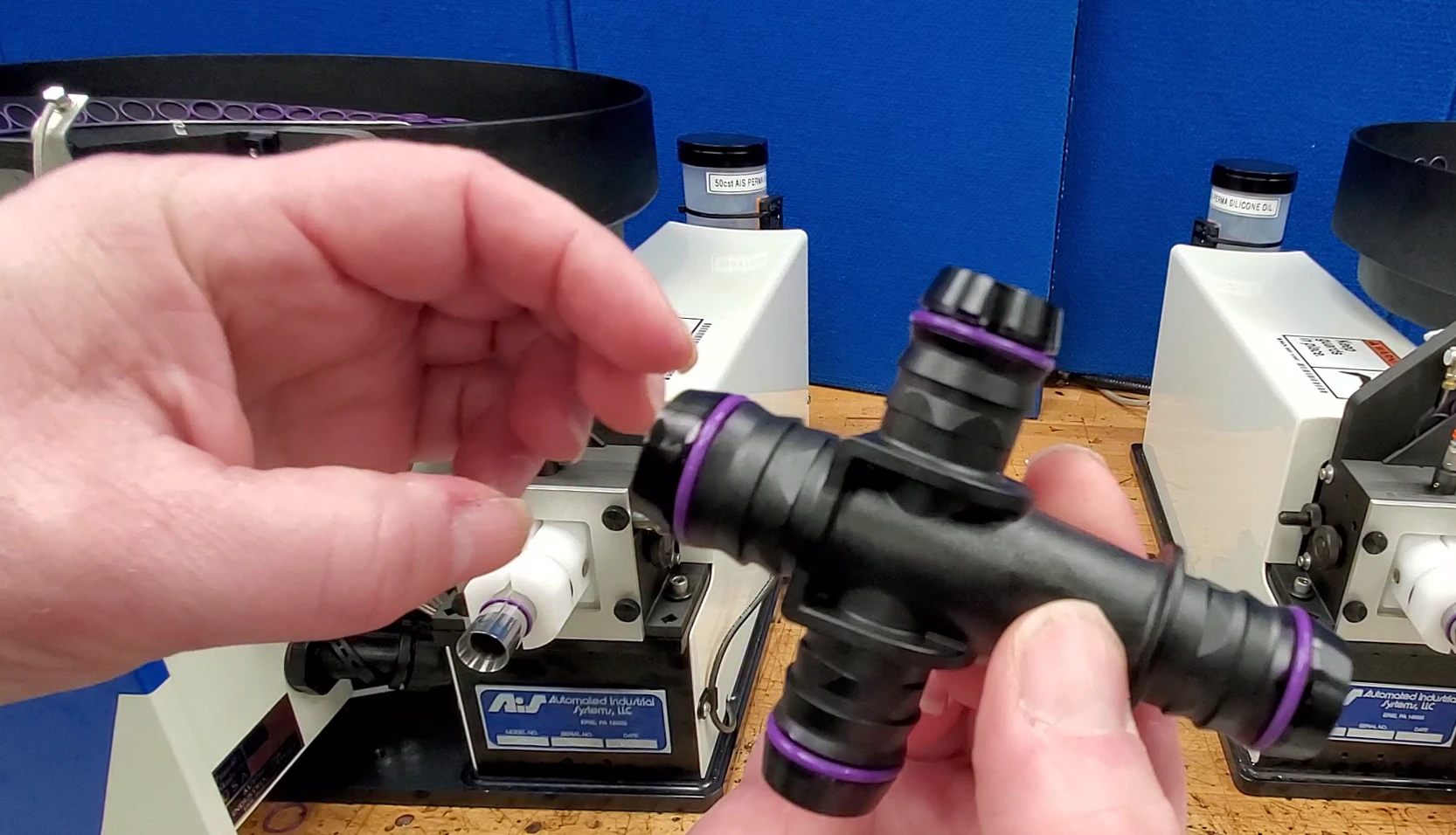
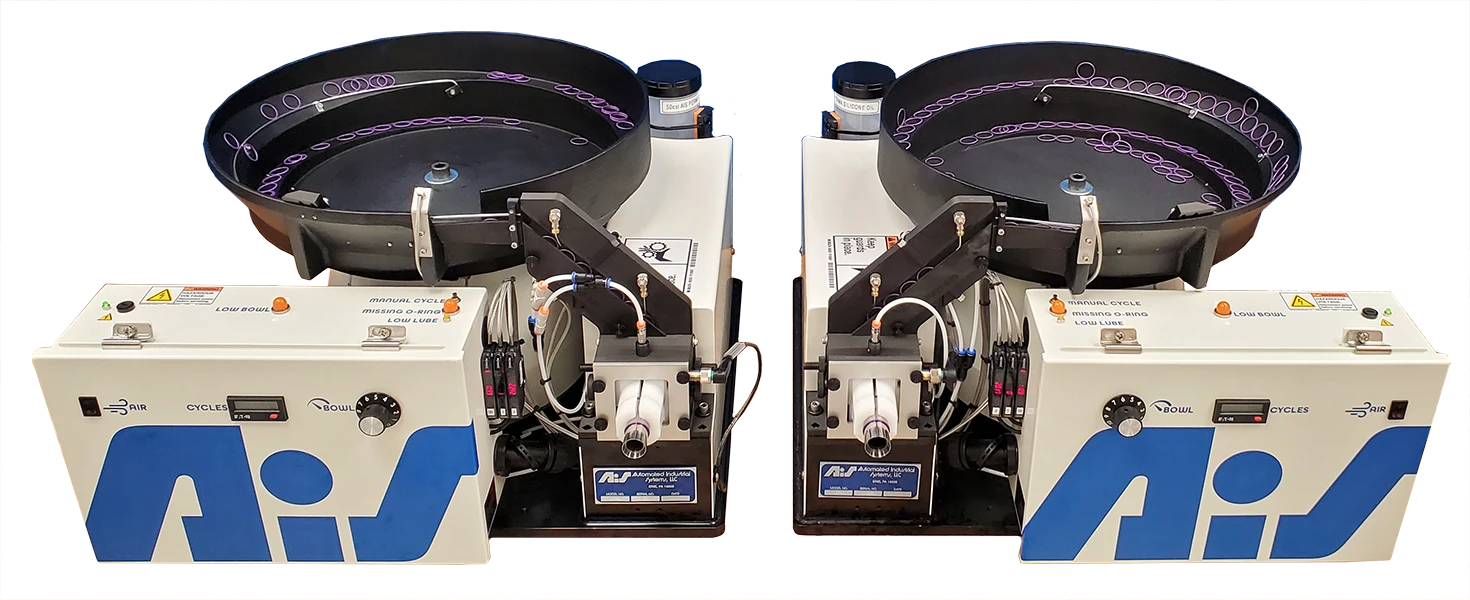
Results / Takeaways
-
High-Volume Efficiency: With this new configuration, the client anticipates significant improvements in daily output, positioning them to better handle rising production demands.
-
Less Rework, Less Waste: The consistent performance of both ASP-1 machines leads to fewer defective parts, saving on materials and labor costs.
-
Future-Ready Production: Having two machines made it easier to scale up if order volumes increased. The client could add shifts or allocate a machine to new parts without sacrificing speed or quality.
By doubling down with both a right and left handed ASP-1, our client could manage two slightly different part requirements without compromising efficiency. The result?
A seamless assembly process with minimal downtime, fewer errors, and high-quality output, an excellent demonstration of how o-ring assembly machines can address complex needs.
Wondering if two ASP-1 machines could streamline your own operation?
Reach out to AIS today for a custom solution that fits your exact needs.